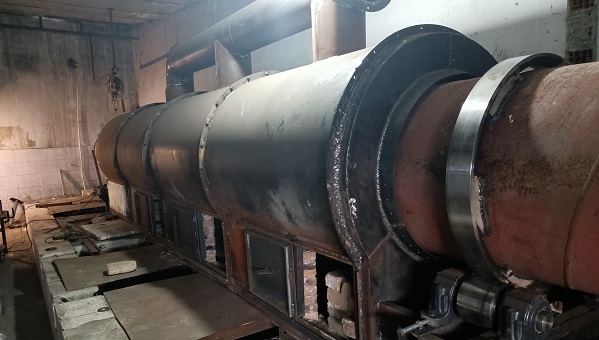
Pyrolysis Reactors
The carbonization process involves heating biomass at 500-600 degrees C in an oxygen-free environment to ensure gasification and carbonization. In this process, a high amount of gasification occurs and our reactors, designed with our R&D studies and experience, offer trouble-free use.
Features:
| ||||||||||||||||||||||||||||
The carbonization (pyrolysis) process is the processing of organic materials at high temperatures in an oxygen-free environment to obtain carbon-rich products. This process is carried out with Stationary and rotary type pyrolysis machines. Stationary type pyrolysis reactors allow the raw material to be pyrolyzed in a fixed environment, under controlled temperature and pressure. Raw materials can generally be materials with high carbon content such as wood, agricultural waste, coal, plastic or organic waste. Fixed type machines are especially suitable for low capacity and certain raw materials.
Rotary type pyrolysis machines have a larger capacity and operate with a system where the raw material is in constant motion. The rotary drum allows the material to be pyrolyzed more homogeneously in a hot gas environment. These machines are flexible enough to process agricultural waste, forest products and various organic wastes and are preferred for large-scale production. In rotary type machines, the material moves continuously in the rotary drum under high temperature, which allows the heat to be distributed evenly.
In both systems, the gas, liquid and solid products produced during pyrolysis are separated. These products are valuable by-products such as biochar (char), biogas and pyrolysis oil. Pyrolysis machines generally operate at 400-700°C and the combustible gases formed during the process can be used in energy production. Each stage in the system requires meticulous control of temperature, pressure and time. As a result, these machines are of great importance for sustainable energy production and recycling of organic waste.