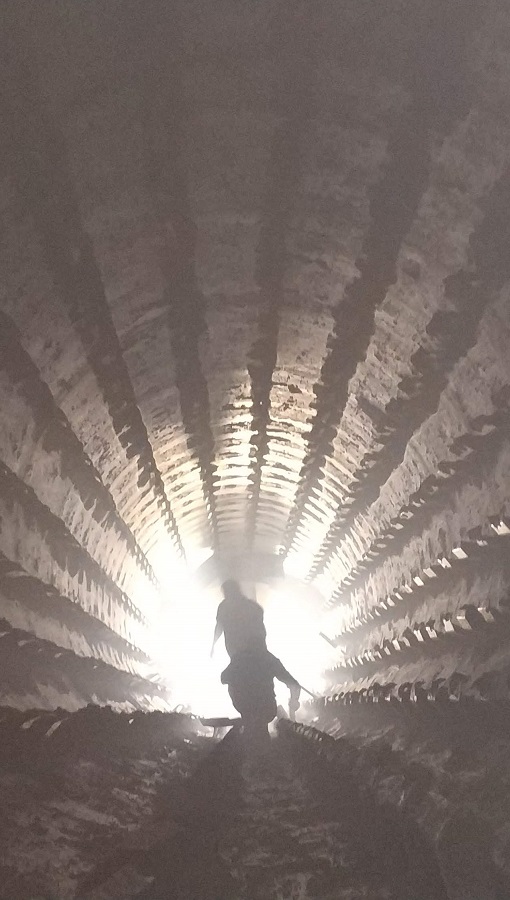
Granulated Fertilizer Production Machinery: Essential Stages for NPK, Organic, and Mineral Fertilizers
Granulated fertilizer production plays a pivotal role in modern agriculture, offering an efficient and effective way to supply essential nutrients to plants. Unlike liquid fertilizers, granulated forms are easier to transport, store, and apply, making them the preferred choice for many farmers and agricultural businesses. To produce high-quality granules, specialized machinery is crucial at each stage of the manufacturing process.
1. Raw Material Mixing for NPK Fertilizer
The production of NPK fertilizers begins with the precise blending of raw materials, including nitrogen (N), phosphorus (P), and potassium (K). These key components are mixed in specific ratios to ensure the fertilizer provides the right balance of nutrients for plant growth. To achieve this, high-efficiency fertilizer mixers are employed. These machines ensure thorough mixing of the raw materials, providing a homogeneous blend that will be formed into granules.
- Recommended Equipment: Fertilizer Mixer, Horizontal Mixer, Vertical Mixer
2. Granulation Process for NPK and Mineral Fertilizers
Once the raw materials are properly mixed, the next step is granulation. Granulation is the process of converting the mixed raw materials into solid granules. This is done through a granulation machine, which shapes the mixture into uniformly sized pellets. The granulation process not only helps in nutrient release but also enhances the shelf-life of the fertilizer.
For NPK fertilizers, the drum granulator or pan granulator is often used. These machines ensure that the granules have a consistent size, allowing for easy application and transport.
- Recommended Equipment: Drum Granulator, Pan Granulator, Disc Granulator
3. Drying for NPK, Organic, and Mineral Fertilizers
After granulation, the fertilizer granules still contain moisture. To prevent clumping and enhance shelf-life, the granules must be dried. Rotary dryers or fluidized bed dryers are commonly used in the fertilizer industry to remove excess moisture from the granules. Drying also ensures that the nutrients in the fertilizer remain stable and effective during storage and transportation.
- Recommended Equipment: Rotary Dryer, Fluidized Bed Dryer, Fertilizer Drying Equipment
4. Cooling Process for NPK, Organic, and Mineral Fertilizers
After drying, granules are still hot and need to be cooled rapidly to avoid shape distortion. The cooling process is essential for maintaining the quality and shape of the granules. Cooling machines, such as counterflow coolers, are used to reduce the temperature of the granules quickly.
This process is crucial for preventing breakage during the later stages of production and ensures the granules remain intact for easier handling and application.
- Recommended Equipment: Counterflow Cooler, Fertilizer Cooler, Granule Cooling Equipment
5. Sieving and Screening for Quality Control
Once cooled, the granules undergo sieving to separate any oversized or undersized granules. This step ensures that only uniform-sized granules reach the final product stage. Vibrating sieves or rotary screens are used to sift out the unwanted particles, which can be recycled back into the production process.
This sieving process guarantees the consistency and quality of the final product, as granule size plays a significant role in the fertilizer's efficiency and ease of application.
- Recommended Equipment: Vibrating Sieve, Rotary Screen, Fertilizer Screening Machine
6. Coating and Additional Treatments (for Specific Fertilizer Types)
For some fertilizer types, such as organic or slow-release fertilizers, an additional step may involve coating the granules with a protective layer. This ensures the slow and controlled release of nutrients over time. Coating machines and spray dryers are used to apply the protective coating and ensure even distribution.
- Recommended Equipment: Fertilizer Coating Machine, Spray Coater
Conclusion: Efficient and Effective Granular Fertilizer Production
Granulated fertilizers, whether NPK, organic, or mineral, require advanced machinery to ensure that the production process is efficient, reliable, and results in high-quality products. From mixing and granulation to drying, cooling, and sieving, each stage plays a critical role in producing a high-performing fertilizer.
By investing in the right machinery—such as granulators, mixers, dryers, coolers, sieves, and coating machines—fertilizer manufacturers can optimize their production process, enhance the quality of their products, and meet the growing demands of the agricultural sector.
If you're looking to enhance your fertilizer production capabilities, we offer a wide range of fertilizer production machines that cater to all stages of the process. Explore our extensive product lineup and find the right machinery for your needs today!
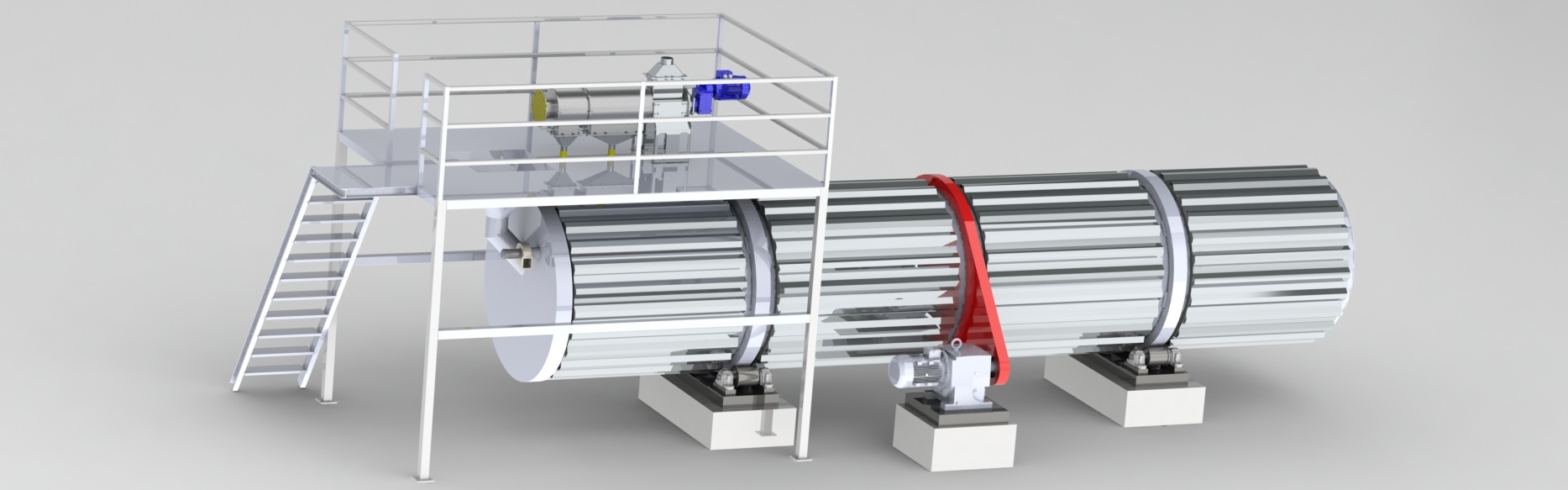